Key Highlights
- What is a Digital Twin? Digital Twin technology creates virtual replicas of physical objects that reflect real-time changes in physical states.
- Core of Industry 4.0: Digital twins integrate IoT, AI, and GPU computing for advanced industrial applications.
- Lifecycle Impact: Digital Twin plays a crucial role throughout the entire product lifecycle, with wide applications from design and production to maintenance.
- Business Benefits: Through real-time data analysis and simulation, digital twin effectively improves production efficiency, reduce costs, and optimizes resource allocation via optimizing production and improving decision-making.
What is a Digital Twin?
A Digital Twin is an advanced virtual model of a physical object or system, enabling real-time data-driven insights, predictive analysis, and automation. More than just a 3D model, a digital twin continuously updates itself based on sensor data, allowing businesses to monitor performance, predict failures, and optimize operations proactively.
With increasing advancements in IoT, AI, and computational power, digital twins are becoming essential tools in smart manufacturing, offering multi-physics, multi-scale simulations that revolutionize industrial processes.
What is a Digital Twin?
A Digital Twin is an advanced virtual model of a physical object or system, enabling real-time data-driven insights, predictive analysis, and automation. More than just a 3D model, a digital twin continuously updates itself based on sensor data, allowing businesses to monitor performance, predict failures, and optimize operations proactively.
With increasing advancements in IoT, AI, and computational power, digital twins are becoming essential tools in smart manufacturing, offering multi-physics, multi-scale simulations that revolutionize industrial processes.
Technical Architecture of a Digital Twin
The architecture of a Digital Twin system typically comprises four main levels, forming a complete data flow and analysis framework from bottom-layer data collection to top-layer application services:
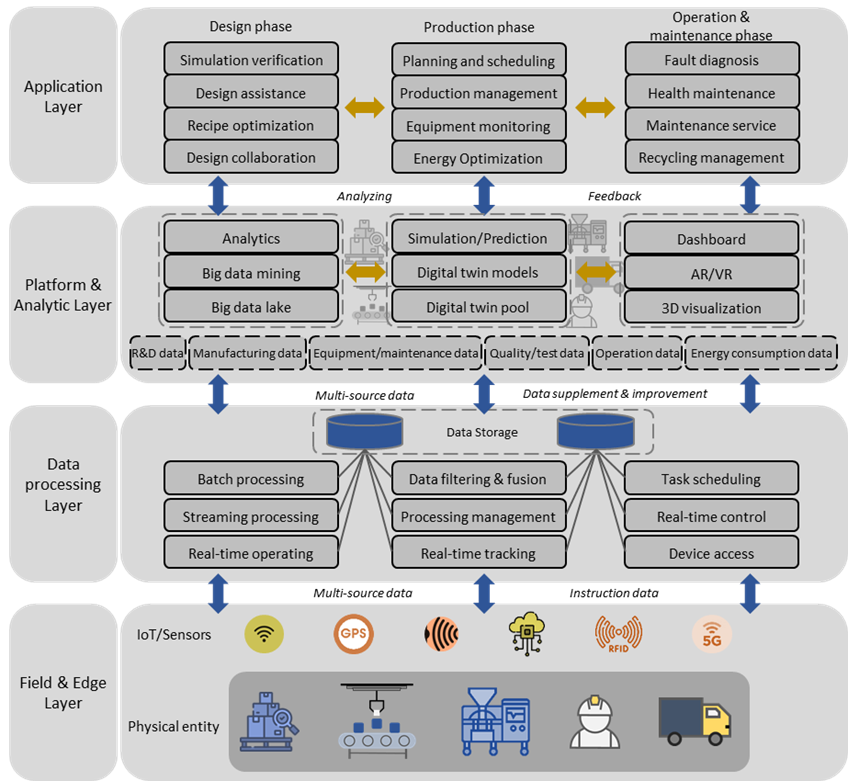
A comprehensive Digital Twin system includes the following key components from bottom to top
1. Physical and Edge Layer:
- Physical devices and IoT sensors collect real-time data.
- Edge computing processes initial information.
- Basic monitoring and control systems ensure stable operations.
2. Data Processing Layer:
- Data cleansing and integration for accurate insights.
- Real-time and batch processing optimize analytics.
- AI-driven anomaly detection ensures system reliability.
3. Platform and Analytics Layer:
- Big Data analytics reveal deep insights.
- Simulation models predict performance and optimize systems.
- AR/VR & 3D visualization enhance interaction with digital twins.
4. Application Layer:
- Smart Design: Digital twins assist in R&D.
- Production Optimization: AI-powered automation improves efficiency.
- Predictive Maintenance: Real-time alerts prevent system failures.
These levels are tightly connected through data flows and feedback mechanisms, forming a closed-loop information circulation system that enhances decision-making at every level of manufacturing.
Key Applications of Digital Twins
1. Smart Manufacturing:
- Real-time machine monitoring improves efficiency.
- Energy consumption analysis optimizes power usage.
- Predictive maintenance reduces downtime.
- Production scheduling optimization enhances output.
2. Supply Chain & Logistics:
- AI-driven supplier coordination ensures timely deliveries.
- Real-time demand forecasting minimizes stock issues.
- Logistics optimization reduces transportation costs.
3. Quality Control & Defect Detection:
- Automated quality checks improve product reliability.
- AI-powered defect detection ensures minimal waste.
- Process improvement suggestions reduce defects.
4. Advanced AI Integration & Automation:
Deep Reinforcement Learning in Production:
In dynamic production scheduling, deep reinforcement learning shows tremendous potential:
- Self-learning intelligent agents optimize scheduling.
- Parallel batch processing speeds up operations.
- Dynamic task scheduling improves adaptability.
Next-Gen AI & Digital Twin Synergy:
Next-generation solutions integrate multiple advanced technologies:
- Genetic algorithms enhance automation.
- Advanced AI models optimize decision-making.
- Multi-agent AI systems enable large-scale industrial applications.
Future Trends in Digital Twin Technology
Digital Twin technology is still in its early stages of application, but as Industry 4.0 advances, its development potential is enormous:
Emerging Technology Integrations:
- AI-powered predictive analytics enhance forecasting accuracy.
- 5G connectivity accelerates real-time data transmission.
- Cloud and Edge computing synergy enables scalable applications.
Expanding Industry Applications:
- Sustainable manufacturing leverages digital twins for energy efficiency.
- Hybrid factory scheduling integrates AI and real-time data.
- Self-adaptive production systems autonomously optimize workflows.
Conclusion: Why Digital Twins Matter for Industry 4.0
Digital Twins are revolutionizing smart manufacturing, offering unparalleled visibility, automation, and predictive intelligence. Businesses adopting digital twins gain a competitive edge in optimizing operations, reducing costs, and driving innovation.
Best Practices for Implementing Digital Twins:
It is recommended that companies adopt a gradual approach when implementing Digital Twin
- Define clear business objectives for digital twin adoption.
- Develop a comprehensive data collection framework.
- Gradually expand applications to maximize value.
- Continuously update and optimize systems to stay ahead.
With proper execution, digital twin technology unlocks immense potential for companies looking to excel in the era of Industry 4.0 and smart manufacturing.